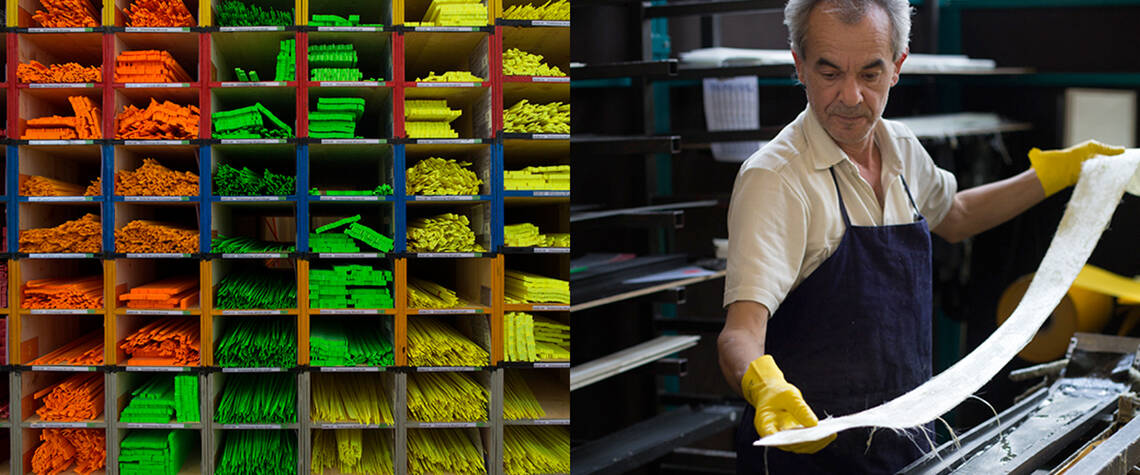
REPORTAGE
Da wird ein Ski draus
In der Skiproduktion muss jedes Detail stimmen. Auch die Embleme. Ein Fabrikbesuch in Mittersill, wo schnelle Bretter die Welt bedeuten.
Im ersten Moment wirkt die Szene verwirrend. Die große Halle im Untergeschoss der Blizzard-Produktion in Mittersill liegt leer und verwaist da. Alles scheint so, als sei es schon lange nicht mehr benutzt worden. Licht dringt nur durch milchige Fenster auf der einen Seite des Raums. Stille.
Für Blizzard-Mann Thorsten Steiner hingegen ist die leere Halle ein gutes Zeichen. Die Firma, die seit mehr als 70 Jahren zu den besten Skiproduzenten der Welt zählt, hat komplett auf Lean Produktion umgestellt. Dabei wird versucht, alle unnötigen Wege, Arbeitsschritte und Materialien zu vermeiden. Heute wird nur noch gelagert, was in Kürze verarbeitet wird – darunter auch unterschiedliche Bauteile der RATHGEBER-Gruppe. „Material, das einfach irgendwo herumsteht, kostet nur Geld, das wollen wir vermeiden“, erklärt Steiner. Angeliefert wird ausschließlich „just in time“. Entsprechend weniger Fläche ist nötig.
Was das bedeutet, zeigt sich im Erdgeschoss des Werks. Hier ist die Stimmung ganz anders: In der großen Halle reihen sich die Arbeitsstationen der einzelnen Fertigungsschritte auf. Es dröhnt und zischt, Elektrokarren schlängeln sich mit ihren Anhängern durch die Gänge und versorgen die einzelnen Arbeitsplätze mit Nachschub.
Zusammengefasst funktioniert die Skiproduktion so: Die Einzelteile für ein Exemplar werden vorbereitet, aufeinandergelegt und am Ende unter großem Druck und Hitze in einer Form miteinander verpresst. Zum Schluss wird überschüssiges Material abgeschnitten, der Ski geschliffen – fertig. In Wahrheit ist das Ganze viel komplizierter, allein die Organisation der Abläufe eine Arbeit, die niemals endet.
Der Prozess beginnt im Rohmateriallager gleich neben der Produktion. Hier werden jeden Tag mehrere Tonnen Material angeliefert, umgeschichtet und für die Fertigung vorbereitet. Auf einer Seite des Lagers stapeln sich Holzlatten, fein geschichtet auf Paletten, bis fast unter das Dach. Im Lager ist es kühl, fast ein wenig ungemütlich. Die Temperatur ist ideal fürs Holz. „Holz lebt. Bis wir es verpresst und verleimt haben, arbeitet es“, sagt Steiner. Holz ist nach wie vor das Material mit dem größten Volumenanteil im Ski. Der Kern bestimmt im Wesentlichen, wie der Ski hinterher funktioniert.
Carbon, Titanal – und immer noch vor allem Holz
Je nach Ski unterscheiden sich die Holzkerne extrem. Ob leichter Tourenski, komfortabler Pistencruiser oder knochenharte Renn-Maschine – die Eigenschaften des fertigen Modells werden maßgeblich vom Holzkern bestimmt. Die Bearbeitung tut das Ihrige: Erst wird der Sidecut herausgeschnitten, um den Ski zu taillieren. Moderne Ski sind vorne und hinten etwas breiter, in der Mitte schmal. Das erhöht den Kantengriff und ermöglicht später das sogenannte Carven, das Schneiden enger Kurven bei hohem Tempo.
„Unsere Zulieferer sind allesamt keine riesigen Konzerne.
Wir setzen sehr stark auf kleinere, flexible Einheiten,“
Thorsten Steiner Marketing-Manager bei Blizzard.
Danach werden die Seitenwangen auf den Ski laminiert. Die Seitenwangen sind nicht nur die sichtbare Seite des fertigen Skis, sie geben auch der Stahlkante den nötigen Halt und ermöglichen so die ideale Kraftübertragung. In einem dritten Schritt wird einmal über den kompletten Holzkern gefräst. Hinterher ist der Ski in der Mitte höher als an den Enden vorne und hinten – nur dadurch kann er auf der Piste genau so flexen, wie es die Entwickler für den jeweiligen Einsatzbereich vorgesehen haben. Ab diesem Moment ist die spätere Form des fertigen Skis schon klar zu sehen.
Zurück ins Lager. „Der Wunschgedanke wäre natürlich, das Material direkt vom Lkw aus zu verarbeiten“, erklärt Blizzard-Mann Steiner. Aber so weit sei man dann doch nicht. So werden täglich palettenweise Holzkerne, Kanten und Seitenwangen zwischengelagert. Weiter hinten sind Beläge und Oberflächen hintereinander aufgeschichtet wie in einem sehr tiefen Supermarktregal. Von vorne wird herausgenommen, von hinten nachgefüllt. So wird nichts alt, die Qualität bleibt hoch: Beläge und Oberflächen, Material für Begurtungen oder Zwischenlagen. Dazu Fleecestoffe für Zwischenlagen, Carbon und Titanal für Einlagen.
Vorteil fürs Familienunternehmen
„Für uns ist es ganz entscheidend, dass auch unsere Zulieferer in diesem System funktionieren“, sagt Thorsten Steiner. Fehle am Tag X auch nur das kleinste Teil, könne man nicht produzieren – der worst case. Auch wegen dieser komplexen Anforderungen sieht Steiner Vorteile für einen flexiblen Partner wie RATHGEBER. „Bei RATHGEBER brauchen wir keine langen Vorlaufzeiten. Und im Zweifel können sie extrem schnell auf Anforderungen reagieren. Wenn ich jedes Emblem, jede Zierleiste oder Plakette jeweils in Asien bestellen müsste, würde das extrem teuer. Und es würde einfach viel zu lange dauern.“
Running Change heißt das, wenn kurzfristig an der Bauweise oder am Design Änderungen vorgenommen werden. Dann muss auch der Zulieferer entsprechend in der Lage sein, zu reagieren und zu helfen. „Da hat ein Familienunternehmen aus der Nähe natürlich Vorteile“, sagt Steiner. Insgesamt gelte: „Unsere Zulieferer sind allesamt keine riesigen Konzerne. Wir setzen sehr stark auf kleinere, flexible Einheiten“ – klassischer Mittelstand eben.
Wie komplex die Anforderungen sind, zeigt sich zum Beispiel an den Kanten. Die sind immer aus Stahl und doch sehr verschieden. Je nach Modell kommen sie unterschiedlich hart, dick oder bearbeitet. Durchgehende massive Kanten werden etwa für Rennski verwendet. Geschlitzte Kanten machen den Ski weicher und komfortabler. Tourenski haben sehr dünne Kanten, das spart Gewicht. Zu den einzelnen Modellen kommen dann noch die unterschiedlichen Längen. Das gilt auch für die Seitenwangen oder die sehr aufwendige Siebdruckerei bei Blizzard. Pro Ski-Design werden fünf bis sieben Siebe benötigt, über alle Längen kommen da schnell 35 bis 40 Siebe pro Modell zusammen.
Wenn die Ski am Ende geschliffen, geprüft, verpackt und etikettiert sind, geht es doch noch einmal ein Stockwerk tiefer. In einem kleinen Teil des ehemaligen Warenlagers stehen die fertigen Ski zu tausenden in langen Reihen und warten auf den Versand. Allerdings nicht lange. Ski, die einfach nur herumstehen, kosten nämlich auch unnötig Geld.